What is Lean Six Sigma?
Research shows that waste, rework, excess inventory, needless complexity and other productivity problems cost manufacturing companies 15 – 25% of sales revenues. These costs are often called the Costs of Poor Quality (COPQ). In service companies, losses are estimated to be closer to 30%. Simply put, Six Sigma is a measure of variability, typically for a given business process.
When a process is performing at Six Sigma levels, output variability is so low that the process is considered to be virtually defect-free. Motorola coined the term “Six Sigma” in the 1980’s as a stretch goal for first-pass product quality. In the 1990’s Six Sigma evolved into a disciplined, structured performance improvement methodology aimed at reducing cost, reducing lead-time, improving profitability and increasing customer satisfaction.
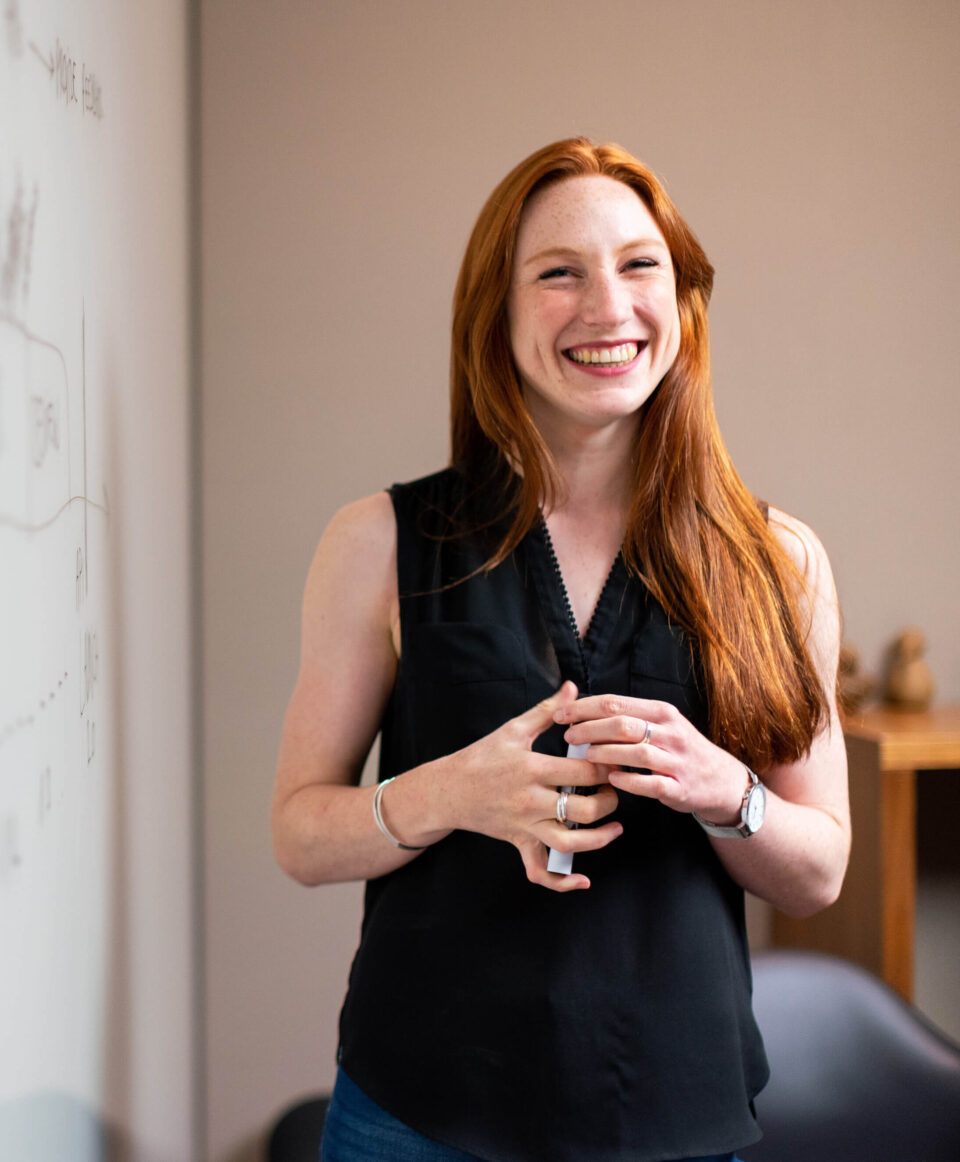
Six Sigma is different from other improvement methodologies in four crucial respects:
- It employs a disciplined, structured approach,
- It is highly data-driven,
- Decisions are made based on objective evidence, and
- It focuses on achieving specific, documented improvements in cost, quality and customer satisfaction.
Although Six Sigma encompasses a large body of knowledge, two of its most powerful tools are applied science and statistical reasoning. Improvement projects are carefully chosen using objective data as the foundation for any improvement-driven activity to ensure a significant Return on Investment (ROI) to the organization.
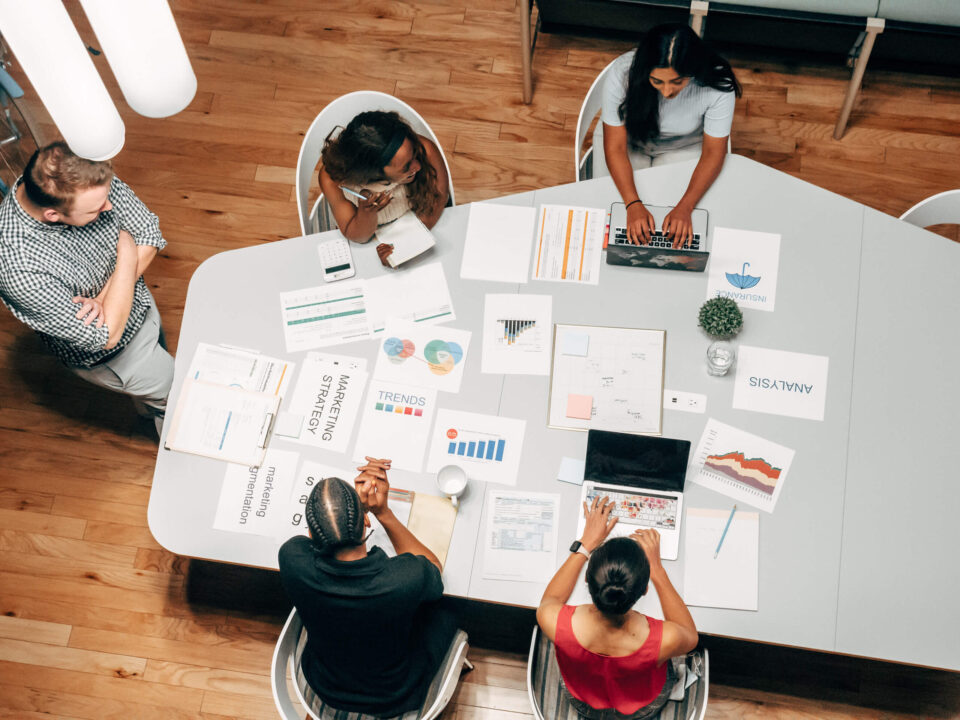
Lean?
The origins of Lean can be found in the innovations of Henry Ford but it is the Toyota Motor Corporation and their single-minded pursuit of waste elimination that has defined Lean performance today. Creating a Lean enterprise simply means providing the greatest value for customers using the fewest resources. Lean applies to any process across the organization and is primarily common sense combined with profound, but often counter-intuitive principles. The methodology and the body of knowledge has been developed and refined over the past 50 years and it is not dependent on systems, software, or technology.
Lean Six Sigma?
Organizations will benefit if they apply one of these powerful methodologies, but those that apply both in an integrated fashion will get the maximum benefit. Six Sigma alone will not eliminate the maximum waste from processes, nor speed the flow of products, services and paperwork. Lean alone will not help you understand the variables affecting product/service performance.
Practitioners of the Six Sigma DMAIC (Define, Measure, Analyze, Improve, Control) framework who are imbued with lean thinking will execute “Lean DMAIC” and save time and effort by avoiding analysis overkill. ETI Group offers a broad range of Lean, Six Sigma and Lean Six Sigma training and consulting support services. Our services are tailored to fit the individual needs of each organization and regardless of where you are in the improvement process we have the skills and experience to help.
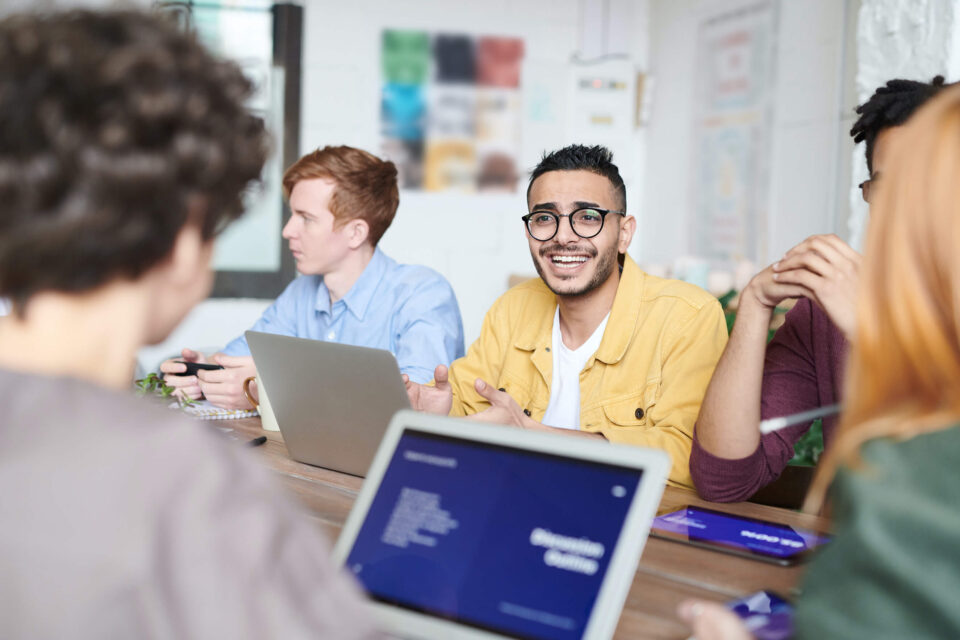
Get Started with Lean 6 Sigma
If you would like more information on how ETI Group can help you with your Lean 6 Sigma needs, we would welcome the opportunity to discuss this with you. Please contact us today!